Appendix L
Making Cup-Leathers
Most handpumps use neoprene or leather seals (cup-leathers) inside the cylinder to force water up the rising main when the piston is moved. When the cup-leathers are worn-out, you will have to pump very hard to make water come out the pump spout and it may come in a small trickle or not at all. If the water level in the rising main is not higher than the water level in the well, there may also be problems with the foot valve (see Section 17). |
Cup-leathers wear-out over time and are the most common problem resulting in handpumps not working anymore. Their effective life depends on the amount of sand being pumped with the water, the smoothness of the cylinder walls and the amount of pump use. Typically, they should be changed every 6-12 months. When cup-leathers wear-out and replacement leathers are not readily available on local markets, pumps are often removed (and destroyed) by villagers trying to access the badly needed well water. |
Villagers dependence on foreign suppliers can be reduced by locally manufacturing cup leathers! Cup-leathers (or "seals") for 5 cm and 6 cm (2 and 2.5 in) diameter cylinders can be made by drawing a leather disk soaked in paraffin wax into a PVC plastic pipe by use of a wood mould and a steel threaded rod, with the use of a threaded handle or crank. The leather disk is formed into a cup shape and then trimmed to size. The cup-leather is then placed on the pump piston and the piston and cup-leather is put back inside the pump cylinder of the appropriate size. |
Steps in making pump cup-leathers:
- The leather should be tanned and about 3 mm or 1 mm (1/8 in or 1/32 in) thick -- better to be thinner than too thick as the leather will swell with wax and then again with water in the pump. The leather should be placed so the rough side is next to the mould and the smooth side is next to the cylinder wall. When cutting the leather disk use a very sharp knife or razor knife pull the leather toward the straight knife edge. Do not saw the leather with the knife, as it's a lot of work and the edge will not come out smooth.
- Soak the leather in hot paraffin wax. Use a double boiler (pan with water on the bottom and another pan or pot on the top to heat the wax in) as you do not want the wax to boil, and there is always danger of it catching on fire. (It should never be left unattended and best done outside). Soak the leather in the hot wax for 15 minutes turning it over several times. If paraffin wax (canning wax) is not available, white candle wax can be used, but in any case the type of wax must be non-toxic.
- Put the leather disk on the wooden mould. The wax and the leather are very hot and care should be taken to have all the equipment ready so no time will be lost and the disk can be put on safely without being burned (it works best with two people). It needs to be done quickly as the wax cools fast and the disk will not draw into the PVC pipe. Again make sure the rough side of the leather is next to the mould and the smooth side is next to the pipe. The leather should be drawn into the PVC pipe (by tightening the handle) until it is just past the tapered portion of the pipe. Let the leather cool for a hour or so.
- Remove the new cup-leather from pipe and mould. Enlarge the centre hole as necessary to snugly fit on the pump piston. Then trim the top edge of the cup leather (the size of the disk was set to have about 3.2 mm (1/8 in) trimmed off the top edge after it is made into a cup-shape). The top edge of the shaped cup leather can be evenly trimmed by removing the wood mould and pushing the leather back into the PVC pipe until just 3 mm (1/8 in) is sticking above the rim of the pipe. It can then be trimmed with a sharp knife. If possible, bevel the edge so that it slopes down towards the inner edge.
- At this point you are ready to put the new cup-leather on the pump piston, and then put the piston with the new cup-leather back in the pump cylinder. If you do not put the pump back together at this time, store the new pump cup-leather in a cylinder (pipe) of the same size as the pump cylinder. As the cup-leather will start to lose its shape it will
not fit in the cylinder and new cup-leathers will need to be made.
2 1/2 INCH CUP-LEATHER FOR 2 1/2 INCH PUMP CYLINDER
(For metric conversions see below):
Leather disk: 3 3/4 inch diameter (1 7/8 inch radius) and 1/8 inch thick + or - 1/32 of a inch. A 3/8 inch hole in the centre of the disk is punched to fit the 3/8 inch threaded rod on the cup-leather maker (Figure 28). After the disk has been formed into a cup shape, about 1/8 inch of rough top edge is trimmed off.
Wood mould block: 2 inch diameter and 3/4 inch thick. This block can be made by using a 21/2 inch power (drill) hole-saw and then filing down to the 2 inch diameter size. A 3/8 inch hole is drilled in the centre of the wood mould to fit on the 3/8 inch threaded rod on the cup-leather maker.
Figure 28: Design for 2.5 Inch Cup-Leathers
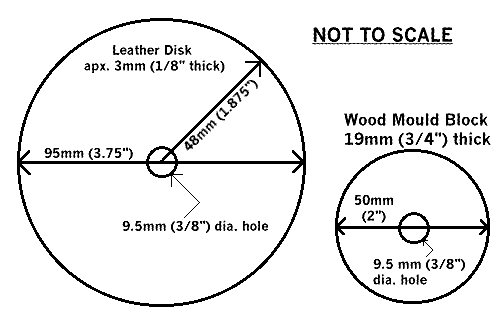
Leather disk: 9.53 cm diameter (4.78 cm radius) and 3.2 mm thick or .3 mm. A 95 mm hole in the centre of the disk is punched to fit the 95 mm threaded rod on the cup-leather maker (Figure 28). After the disk has been formed into a cup shape, about 3.2 mm of rough top edge is trimmed off.
Wood mould block: 5 cm diameter and 2 cm thick. This block can be made by using a 6 cm power (drill) hole-saw and then filing down to the 5 cm diameter size. A 95 cm hole is drilled in the centre of the wood mould to fit on the 95 cm threaded rod on the cup-leather maker.
2 INCH CUP-LEATHER FOR 2 INCH PUMP CYLINDER
Leather disk: 3 5/6 inch diameter (1 21/32 inch radius) and 1/8 inch thick + or - 1/32 inch. A 3/8 inch hole in the centre of the disk is punched to fit the 3/8 inch threaded rod on the cup-leather maker (Figure 29). After disk has been formed into cup shape about 1/8 inch of rough top edge is trimmed off.
Wood mould block: 1 5/8 diameter and 3/4 inch thick. This block can be made by using a 13/4 inch power (drill) hole-saw. Then drill a 3/8 inch hole in the centre to fit on the 3/8 inch threaded rod.
Figure 29: Design for 2 Inch Cup-Leathers
Leather disk: 9.74 cm diameter (4.21 radius) and 3.2 mm thick or 0.3 mm. A 95 mm hole in the centre of the disk is punched to fit the 95 mm threaded rod on the cup-leather maker (Figure 29). After disk has been formed into cup shape about 3.2 mm of rough top edge is trimmed off.
Wood mould block: 4.13 cm diameter and 1.91 cm thick. This block can be made by using a 4.45 cm power (drill) hole-saw. Then drill a 95 mm hole in the centre to fit on the 95 mm threaded rod.

Choose Another Well Construction Module:
|